In the bustling realm of industrial operations, where efficiency and reliability are paramount, even the smallest of components can have a monumental role to play. Strainers are unassuming devices that serve as the first line of defense, ensuring the seamless operation of complex machinery and pipelines. In this blog, we’ll be immersing ourselves in the world of industrial strainers, offering essential installation tips and highlighting the extensive benefits they confer upon heavy-duty operations. From safeguarding critical equipment to optimizing workflow, strainers stand as an indispensable asset in any industrial environment. Join us as we navigate through the key facets of strainer success, arming you with the knowledge to enhance operational efficiency and reap the multitude of benefits they bring to industrial settings.
What are the many benefits of using industrial strainers?
Debris Removal: Industrial strainers act as a filter, preventing larger particles and debris from entering pipelines, which can cause clogs, damage equipment, and disrupt processes.
Equipment Protection: Strainers serve as a safeguard for pumps, valves, and other sensitive machinery by preventing damage from foreign objects or particles.
Extended Equipment Lifespan: By reducing wear and tear on machinery, strainers help prolong the life of expensive industrial equipment, ultimately saving on maintenance and replacement costs.
Improved Process Efficiency: Strainers maintain consistent flow rates and reduce the risk of pressure drops or flow disruptions, ensuring that processes run smoothly and efficiently.
Reduced Downtime: Regular maintenance and cleaning of strainers can prevent unexpected downtime caused by clogs or equipment failure, thereby enhancing overall productivity.
Compliance with Regulations: Strainers can aid in meeting environmental and safety regulations by preventing contaminants from entering sensitive areas or water systems.
Enhanced Product Quality: In industries like oil & gas, and petrochemicals, strainers are crucial for ensuring that products meet high-quality standards by removing unwanted particles.
Cost Savings: Preventing damage to equipment and reducing downtime can lead to significant cost savings over time.
Prevention of Corrosion: Strainers can help prevent corrosion in pipelines and equipment by filtering out corrosive particles.
Customization and Adaptability: Industrial strainers come in various types and materials, allowing them to be tailored to specific industry needs and conditions.
Safety: Strainers contribute to a safer working environment by reducing the risk of equipment failure or accidents caused by foreign objects.
Improved Water Quality: In industries that rely on water, such as power generation or water treatment, strainers help maintain the purity of the water supply.
Is there a list of installation tips for using the industrial strainer?
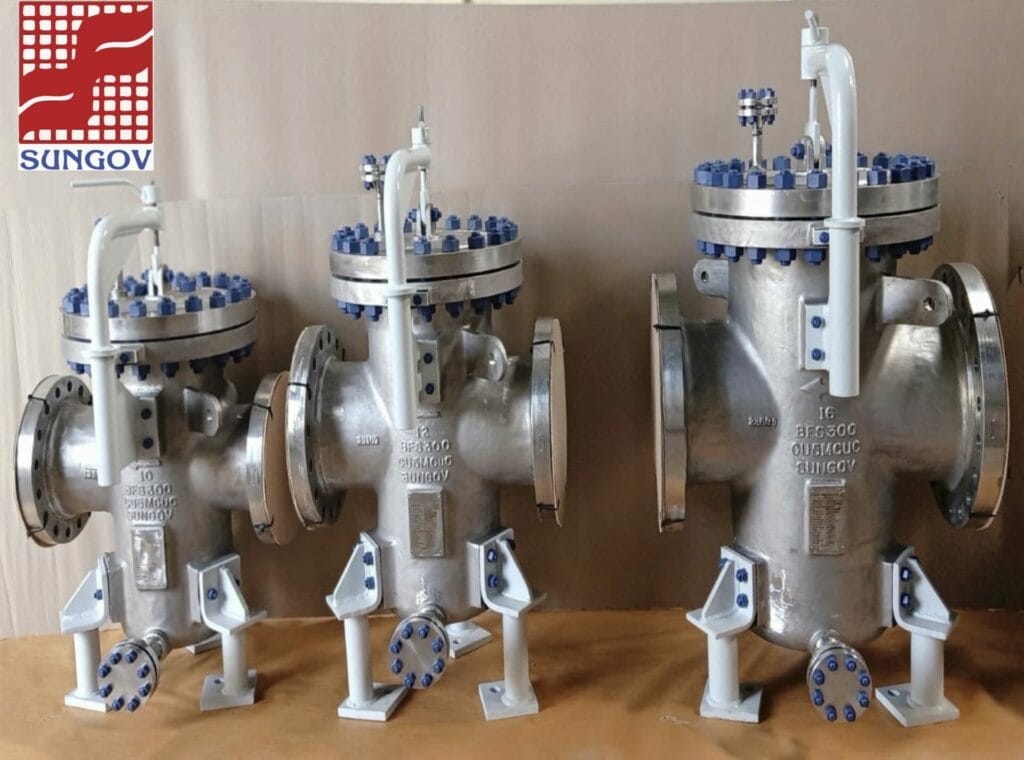
We have listed a few strainer installation tips for you to ensure that the installed industrial strainer works efficiently and effectively and provides you with the benefits it is designed to deliver.
Select the Right Location:
Choose a location in the pipeline where the strainer can effectively capture debris without causing flow disruptions.
Consider Accessibility for Maintenance:
Ensure that the strainer is easily accessible for inspection, cleaning, and maintenance. This will prevent downtime and ensure optimal performance.
Proper Orientation:
Install the strainer with the flow arrow pointing in the correct direction. This ensures that the strainer functions as intended.
Use Proper Gaskets and Seals:
Ensure that high-quality gaskets and seals are used to prevent leaks and maintain the integrity of the system.
Secure Mounting:
Properly anchor and support the strainer to prevent any movement or shifting during operation.
Consider Backwash or Bypass Options:
Depending on the system, consider including backwash or bypass mechanisms to allow for cleaning or temporary bypassing if needed.
Size Appropriately:
Select a strainer size that matches the diameter of the pipeline to avoid flow restrictions and pressure drops.
Check for Alignment:
Ensure that the strainer and connecting pipes are aligned correctly to prevent stress on the strainer body.
Use Proper Fasteners and Hardware:
Select corrosion-resistant fasteners and hardware to prevent deterioration over time.
Maintain Proper Clearances:
Ensure that there is enough space around the strainer for easy access and maintenance.
Consider Pressure Ratings:
Select a strainer with an appropriate pressure rating to handle the expected operating conditions.
Inspect for Damage:
Before installation, carefully inspect the strainer for any signs of damage or defects that may affect performance.
Follow the Manufacturer’s Recommendations:
Adhere to the manufacturer’s installation guidelines and recommendations to ensure proper function and warranty coverage.
Perform Pressure Tests:
Conduct pressure tests after installation to verify that the strainer is properly sealed and can withstand the anticipated pressures.
Document Installation Details:
Keep detailed records of the strainer’s installation, including location, orientation, and any special considerations.
How can the industrial strainers manufactured by Sungov Engineering help you meet the evolving needs?
Sungov Engineering typically focuses on several key innovations to improve its products and meet the evolving needs of its customers. Here are some common considerations:
Material Selection: Materials that are used are durable, corrosion-resistant, and compatible with the fluids being strained. We have even explored advanced alloys, polymers, and coatings to enhance performance.
Advanced Filtration Technology: Innovations in filtration media and techniques allow for more efficient removal of particles, debris, and contaminants from fluids. This can involve using finer mesh sizes or specialized filter media.
Design and Engineering: Manufacturers work on optimizing the design of strainers for specific applications. This includes considerations for flow rates, pressure drops, and installation requirements. Computational tools and simulations aid in this process.
Automation and Control: Integrating automation features like self-cleaning mechanisms, differential pressure sensors, and remote monitoring capabilities can improve the efficiency and reliability of strainers.
Ease of Maintenance: Manufacturers aim to design strainers that are easy to inspect, clean, and maintain. Quick-opening closures, self-cleaning mechanisms, and user-friendly components are examples of innovations in this area.
Adaptability to Various Fluids: Strainers may need to handle a wide range of fluids with different viscosities, temperatures, and chemical compositions. Sungov Engineering seek to develop strainers that can effectively filter various types of fluids.
Environmental Considerations: Innovations in materials and processes aim to reduce the environmental impact of strainer manufacturing and operation. This may involve using recyclable materials or designing strainers with lower energy consumption.
Customization and Flexibility: Sungov Engineering strives to offer products that can be customized to meet specific customer requirements. This might involve tailoring the size, configuration, and features of the strainer to suit unique applications.
Compliance with Standards and Regulations: Sungov Engineering stays updated on industry standards and regulations related to strainer design and performance. Adhering to these standards ensures that their products meet safety and quality requirements.
Cost-Effectiveness: Sungov Engineering works to balance innovation with cost-effectiveness. This may involve finding ways to reduce production costs while maintaining or improving product quality and performance.